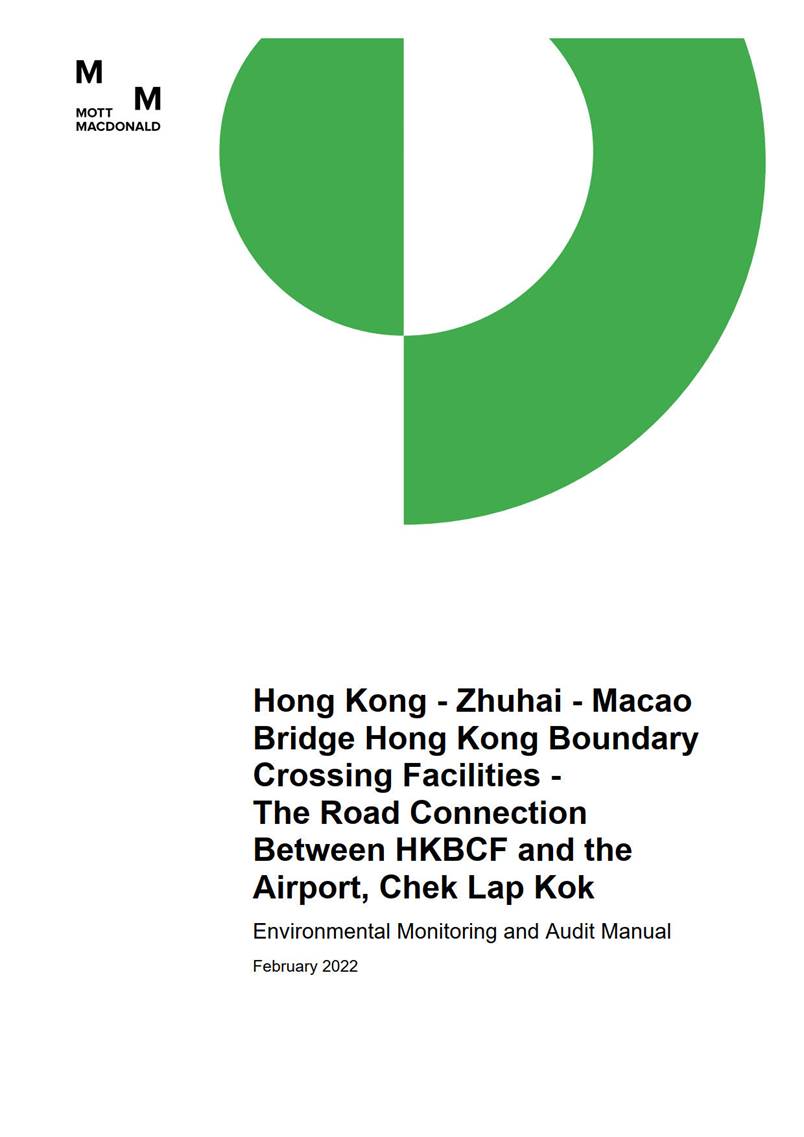
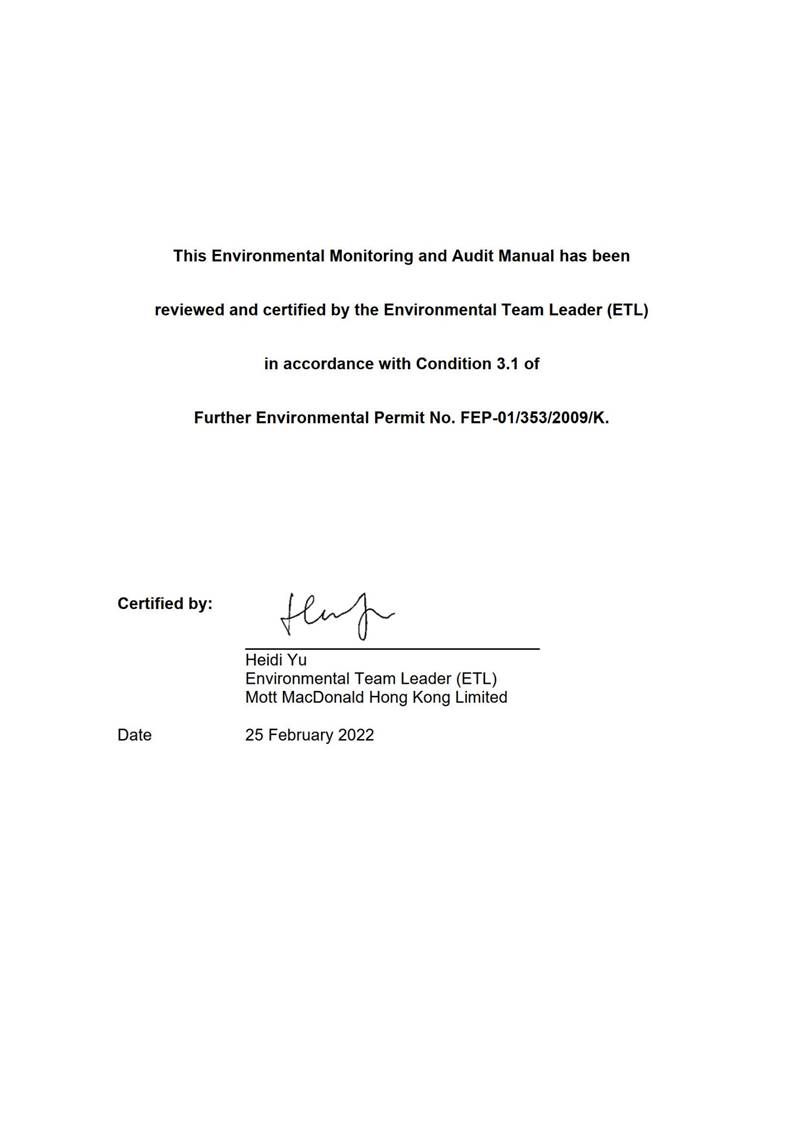
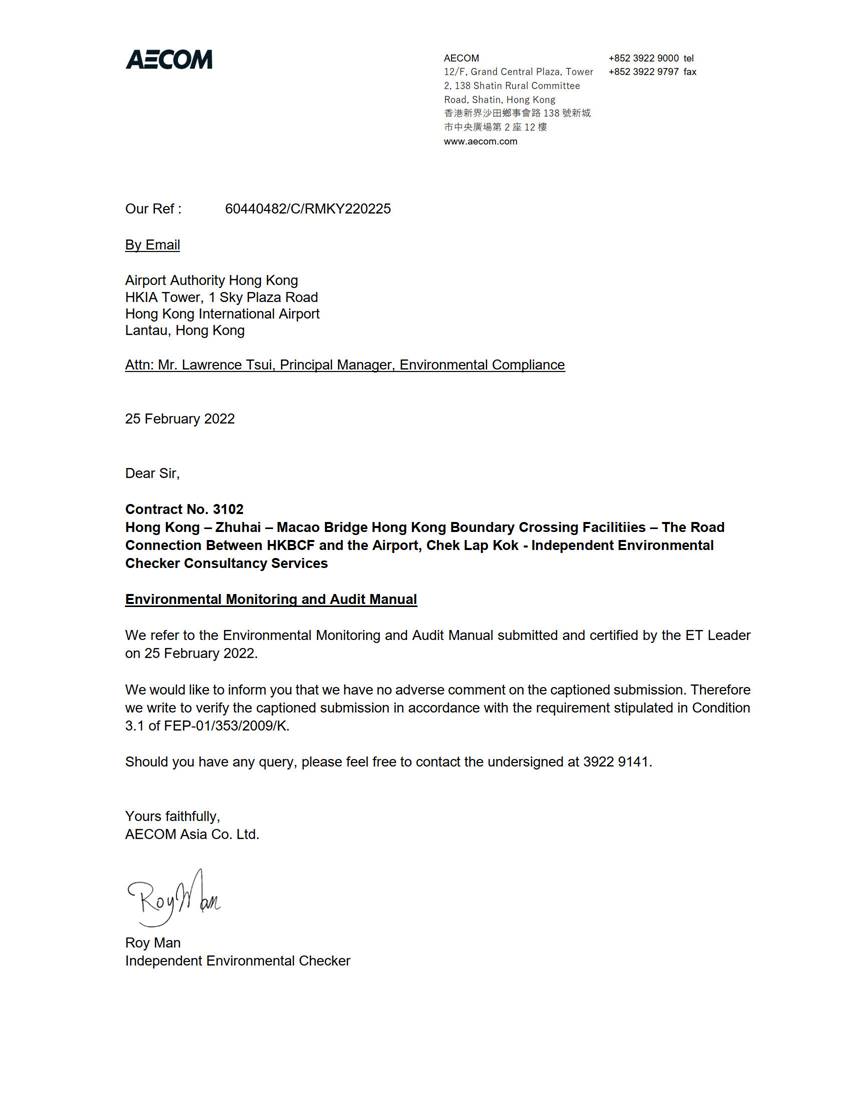
Contents
1
Introduction
2
Project Description
3
Environmental Submissions
4
Air Quality
5
Noise
6
Sediment Quality
7
Waste Management
8
Water Quality
9
Ecology
10
Fisheries
11
Cultural Heritage
12
Hazard To Life
13
Landscape & Visual
14
Site Environmental Audit
15
Reporting
Figure 1
Project Location
Appendix A.
Tentative Construction Programme
Appendix B.
Environmental Mitigation Implementation Schedule
Tables
Table 6.1: Universal Treatment Standards (UTS) for Reuse
of Sediment Treated by Cement Mixing and Stabilization 9
Table 7.1: Waste Management Checklist 12
Table 13.1: Monitoring Programme 19
Table 13.2: Mitigation Measures during
Construction and Operation Phases 20
Table 13.3: Event and Action Plan 21
1 Introduction
1.1
Background
1.1.1 To connect the Hong Kong-Zhuhai-Macao Bridge (HZMB) Hong
Kong Boundary Crossing Facilities (HKBCF) with the Hong Kong International
Airport (HKIA), roads including an elevated bridge structure (hereinafter referred
to as “the HKBCF Viaduct/Roads”) were proposed as part of the HKBCF project, as
described in Section 4.5 of the approved Environmental Impact Assessment (EIA)
report of the HKBCF project. The HKBCF Viaduct/Roads are located partly within
the boundary of the Airport Island near Terminal 2 (T2) and partly within the
boundary of the land corridor between HKBCF and the Airport Island, i.e. partly within the HKBCF boundary.
1.1.2 Under the HKBCF project, the arrangements for the planning
of the construction of the HKBCF Viaduct/Roads were formulated based on the
scenario with the existing two-runway system (2RS) at the HKIA. The portion of
the HKBCF Viaduct/Roads falling within the boundary of the land corridor
between HKBCF and HKIA were originally planned to be constructed by Highways
Department (HyD) of the Government of the Hong Kong
Special Administrative Region (HKSARG) as part of the HKBCF project.
1.1.3 With the planned expansion of HKIA into a three-runway
system (3RS), a revised layout of the HKBCF Viaduct/Roads (the revised layout
is hereinafter referred to as the proposed “HKIA-HKBCF Road Connection”) was
formulated as part of the P282 Terminal 2 Expansion Design Consultancy of
Airport Authority Hong Kong (AAHK). The proposed HKIA-HKBCF Road Connection has
taken into account the design of the 3RS road network
designed around the expanded T2 building. In addition to preparing the detailed
design, it was also considered that the proposed HKIA-HKBCF Road Connection
within the HKBCF boundary would be constructed by AAHK instead of HyD along with the 3RS road network planned within the
Airport Island. Upon completion of the construction works, the new HKIA-HKBCF
Road Connection outside the Airport Island would be handed over to HyD for future operation and maintenance.
1.1.4 The EIA for the HKBCF project, which covered the HKBCF
Viaduct/Roads as a Designated Project (DP) based on the requirements set out in
Item A.8. (i.e., A road bridge more than 100m in length between abutments) in
Part 1 of Schedule 2 to the Environmental Impact Assessment Ordinance (EIAO)
(Cap. 499), was completed and approved (EIA Register No.: AEIAR-145/2009) and
an Environmental Permit (EP) (EP No.: EP-353/2009) was granted under the EIAO
to HyD.
1.1.5 On the other hand, the 3RS EIA had subsequently commenced
and completed (EIA Register No.: AEIAR-185/2014) by AAHK, and it has already
taken the layout of the proposed HKIA-HKBCF Road Connection into account and
has assessed the relevant cumulative environmental impacts. The planned change
in implementation agent from HyD to AAHK for the
construction of the proposed HKIA-HKBCF Road Connection outside the Airport
Island would involve a transfer of corresponding responsibilities under the
HKBCF EP from HyD to AAHK. To this end, an
Environmental Review Report (ERR) was prepared and submitted to EPD in November
2018 which concluded that the change of implementation agent form HyD to AAHK for the construction of HKIA-HKBCF Road
Connection would not result in any exceedance or violation of the environmental
performance requirements set out in the approved HKBCF and 3RS EIAs and the
mitigation measures identified in these EIAs remained relevant and valid. A
Further Environmental Permit (EP No. FEP-01/353/2009/K) for the construction of
the HKIA-HKBCF Road Connection was granted to AAHK in December 2018 in
accordance with Section 12 of EIAO.
1.2
Purpose of the
Manual
1.2.1 This Environmental Monitoring and Audit (EM&A) Manual
outlines the monitoring and audit programme proposed for the HKIA-HKBCF Road
Connection (hereafter referred to as the Project). In accordance with Condition
3.1 of Further Environmental Permit (FEP) (EP No. FEP-01/353/2009/K), an
updated EM&A Manual shall be prepared before the commencement of
construction works.
1.2.2 The purpose of this EM&A Manual (hereafter referred to
as the Manual) is to guide the setup of an EM&A programme to ensure
compliance with the recommendations in the approved Environmental Impact
Assessment (EIA) Report of Hong Kong - Zhuhai - Macao Bridge Hong Kong Boundary
Crossing Facilities – Investigation (hereinafter referred to as “the EIA
Report”) and the findings from the ERR, to summarize appropriate EM&A
requirements in accordance with the information and recommendations described
in the EIA Report and by taking into account any specific site conditions that
may be changed before the construction of HKIA-HKBCF Road Connection.
1.2.3 This Manual is prepared by making
reference to the framework of the EM&A Manual of the HZMB HKBCF –
Investigation and the information and recommendation as described in ERR as
approved by EPD. AAHK is the implementation agent for the construction of
HKIA-HKBCF Road Connection and the duties for EM&A works have been
presented in this Manual.
1.2.4 In this updated submission, Section 6 incorporates the
revised quantity of marine sediment to be excavated as estimated by the
Contractor. Section 13 incorporates the latest change on the landscape planting
proposal.
2 Project
Description
2.1.1 The Project will consist of the construction of a road
bridge more than 100m in length between abutments connecting between HKBCF and
the HKIA which is part of the work for HZMB-HKBCF. The location of Project is
shown in Figure 1. The proposed construction
programme of the Project is provided in Appendix A.
The FEP required that an Environmental Team (ET) shall not be in any way an
associated body of the Contractor and Independent Environmental Checker (IEC)
for the Project. ET shall be headed by an ET Leader who has at least
seven years of experience in EM&A or environmental management.
2.1.2 The FEP also required that the IEC shall not be in any way
an associated body of the Contractor and ET for the Project. IEC shall have at
least seven years of experience in EM&A or environmental management.
2.1.3 The responsibilities of respective parties are:
2.1.3.1
Project
Manager (PM) or the PM’s Representative of AAHK
·
supervise the Contractor’s activities and ensure that the requirements
in the Manual are fully complied with;
·
employ ET to implement the EM&A Programme; and
·
employ IEC to audit the results of the EM&A works carried out by the
ET.
2.1.3.2 The Contractor
·
comply with relevant contract conditions and specifications on
environmental protection;
·
provide assistance to ET in carrying out monitoring and site inspection;
·
participate the site inspection undertaken by the ET and IEC; and
undertake any corrective actions;
·
provide information / advice to the ET regrading works programme and
activities which may contribute to the generation of adverse environmental impacts;
·
submit proposals on mitigation measures to reduce environmental impacts;
·
implement measures to reduce environmental impacts where necessary; and
·
adhere to the agreed procedures for carrying out complaint investigation
2.1.3.3 Environmental Team
·
review the success of EM&A programme to cost-effectively confirm the
adequacy of mitigation measures implemented and the validity of the EIA
predictions and to identify any adverse environmental impacts arising;
·
carry out site inspection to investigate and audit the Contractors' site
practice, equipment and work methodologies with respect to pollution control
and environmental mitigation, and take proactive actions to pre-empt problems;
·
audit and prepare audit reports on the site environmental conditions;
·
report on the environmental monitoring and audit results to the PM, IEC
and EPD;
·
undertake regular on-site audits/inspections and report to the PM of any
potential non-compliance;
·
follow up and close out non-compliance actions;
·
keep a contemporaneous log-book of each and
every instance or circumstance or change of circumstances, which may affect the
compliance with the recommendations of the EIA Report and the FEP. The log-book shall be kept readily available for inspection by
all persons assisting in supervision of the implementation of the
recommendations of the EIA Report and FEP or by the Director or his authorized
officers; and
·
notify the IEC within one working day of the occurrence of any such
instance or circumstance or change of circumstances.
2.1.3.4 Independent Environmental
Checker
·
review the EM&A works performed by the ET (at not less than monthly
intervals);
·
audit the monitoring activities and results (at not less than monthly
intervals);
·
report the audit results to the PM;
·
review the EM&A reports (monthly and quarterly EM&A reports)
submitted by the ET;
·
verify the submissions required in the EM&A Manual and FEP;
·
review the proposal on mitigation measures submitted by the Contractor;
·
check the mitigation measures that have been recommended in the EIA and
this Manual, and ensure they are properly implemented in a timely manner, when necessary;
·
verify the environmental acceptability of permanent and temporary works
and relevant design plans;
·
report the findings of site inspections and other environmental
performance reviews to PM; and
·
verify the log-book as maintained by ET.
3 Environmental
Submissions
3.1
Introduction
3.1.1 According to the requirements as stipulated in the FEP and
Section 3.3.3 of the ERR, the Management Organization of Main Construction
Companies, Landscape and Visual Plan (L&V Plan), Waste Management Plan
(WMP), Environmental Management Plan (EMP) and Construction Method Statement
shall be prepared.
3.2
Management
Organization of Main Construction Companies
3.2.1 As per Condition 2.3 of FEP, AAHK shall include the management
organization of the main construction companies and/or any form of joint
ventures associated with the construction of the corresponding part of the
Project and deposit to EPD at least two weeks before the commencement of
construction of each relevant contract under the Project. The submitted
information shall include at least an organization chart, names of responsible
persons and their contact details.
3.3
Landscape and
Visual Plan
3.3.1 As per the Condition 2.4 of the FEP, AAHK shall deposit an
L&V Plan to EPD at least one month before the commencement
of construction of relevant part of the Project. The L&V Plan shall incorporate aesthetic architectural design on
buildings structures and related infrastructure of the Project, streetscape
elements, planting proposals and other measures including night-time lighting
control.
3.4
Waste Management
Plan
3.4.1 As per the Condition 2.5 of the FEP, AAHK shall deposit a
WMP to EPD at least one month before the commencement of the construction of
the Project. The WMP shall describe the arrangements for avoidance, reuse,
recovery and recycling, storage, collection, treatment
and disposal of different categories of waste to be generated from the
construction activities and shall include the recommended mitigation measures
on waste management in the EIA Report. The WMP should indicate the
disposal locations(s) of all surplus excavated spoil and other waste. A trip
ticket system shall be included in the WMP. All measures recommended in the WMP
shall be fully and properly implemented.
3.4.2 The Contractor should adopt this WMP as a basis to develop
their own contract-specific WMPs. The contract-specific WMPs should be updated from time to time
and submitted to the ET and IEC for their verification and AAHK for agreement.
3.5
Environmental
Management Plan
3.5.1 A systematic EMP shall be prepared by the Contractor to
ensure effective implementation of the mitigation measures, monitoring and
remedial requirements presented in the EIA, EM&A and Environmental
Mitigation Implementation Schedule (EMIS). ET and IEC will audit the
implementation status against the EMP and advise the necessary remedial actions
required. These remedial actions shall be enforced by the PM through
contractual means.
3.5.2 The Contractor shall define in details
in the EMP how to implement the recommended mitigation measures in order to
achieve the environmental performance defined in the Hong Kong environmental
legislation and the EIA documentation.
3.5.3 The review of on-site environmental performance shall be
undertaken by ET and IEC through a systematic checklist and audit once the
construction commences. The environmental performance review programme
comprises a regular assessment on the effectiveness of the EMP. Reference
shall be made to ETWBTC 19 / 2005 “Environmental Management on Construction
Sites” or its latest versions, and any other relevant Technical Circulars.
3.6
Construction
Method Statement
3.6.1 In case the Contractor would like to adopt alternative
construction methods or implementation schedules, it is required to submit
details of methodology and equipment to the PM for approval before the work
commences. Any changes in construction method shall be reflected in a
revised EMP or the Contractor will be required to demonstrate the manner in which the EMP should accommodate the proposed
changes.
4 Air
Quality
4.1
General
4.1.1 As the Project will involve only construction of HKIA-HKBCF
Road Connection on the reclaimed land already formed under the HKBCF project,
the construction dust and emissions from construction works of this nature and
size would be limited. According to the ERR, with the implementation of the
recommended mitigation measures in Section 5.2, the construction phase air
quality at all identified air sensitive receivers would comply with the Air
Quality Objectives and no adverse air quality impacts would be anticipated from
the construction of the Project. In view of the above, no air quality monitoring
during the construction phase of the Project is proposed.
4.2
Mitigation
Measures
4.2.1 Condition 2.6 of the FEP has stipulated that watering shall
be undertaken at least eight times per day on all exposed soil within the
Project site and associated work areas throughout the construction period. In
addition, relevant dust control measures such as surfaced with crushed stone or
coarse gravel on the temporary access road, enclosure for handling of dusty
materials, and wheel wash facilities recommended in the EIA Report shall be
implemented to minimise generation of dust. All relevant mitigation measures
are summarised in the Environmental Mitigation Implementation Schedule (EMIS)
in Appendix B.
5 Noise
5.1
General
5.1.1 According to the EIA Report, the nearest noise sensitive
receivers (NSRs) from the Project is located in the
existing Tung Chung New Town at distance of about 2 km from the construction
work site of the Project. Given the large separation distance between the works
area and the NSRs, no adverse construction noise impact would arise with
appropriate mitigation measures in place. In view of the above, no noise
monitoring during the construction phase of the Project is proposed.
5.2
Mitigation
Measures
5.2.1 The EIA Report recommended construction noise control
measures including:
·
good site practices to limit noise emissions at the sources;
·
use of quiet plant and working methods;
·
use of site hoarding as noise barrier to screen noise at ground level of
NSRs;
·
use of shrouds/ temporary noise barriers to screen noise from relatively
static powered mechanical equipment (PME);
·
scheduling of construction works outside school examination periods in
critical area; and
·
alternative use of plant items within one worksite, wherever
practicable.
5.2.2 Relevant mitigation measures are summarised in the EMIS in Appendix B.
6 Sediment
Quality
6.1
General
6.1.1 Based on the EIA Report and the Environment, Transport and
Works Bureau Technical Circular (Works) (ETWB TCW) No. 34/2002 on the
Management of Dredge/Excavated Sediment, the marine sediments arising from the
works within the Project works area were Category L sediments and Category M
sediments that had passed the biological screening, which could be handled
through open sea disposal and open sea disposal at dedicated sites
respectively. In accordance with the
Condition 3.27 of the EP (EP No.: EP-353-2009/K), if any off-site disposal is
required, the excavated marine sediment shall be disposed of at the designated
disposal sites within Hong Kong as allocated by the Marine Fill Committee or
other locations as agreed by EPD. The
procedures for seeking disposal shall comply with requirements provided in ETWB
TCW No. 34/2002.
6.1.2 According to the Contractor, the volume of marine sediment
to be excavated from the construction of the foundations of the Project would
be about 4,500 m3. It is recommended that these marine sediments
excavated may be treated using cement/ solidification/ stabilization techniques
and reused onsite or offsite for backfilling and/or landscaping so that the
need for offsite disposal is avoided as far as practicable. As the location where the treated marine
sediment to be re-used has yet to be confirmed at the time of the preparation
of this manual, it is subject to the final construction design.
6.1.3 The treated marine sediments using
cement/solidification/stabilization techniques should be tested against the
Toxicity Characteristics Leaching Procedure (TCLP) (as shown in Table 6.1) which were recommended in the EPD’s Practice
Guide for Investigation and Remediation of Contaminated Land. The
treated sediment should also be tested against relevant engineering
requirements to confirm their suitability as backfilling material for
respective areas of different future uses. Unconfined Compressive Strength
(UCS) will be tested and defined based on respective engineering requirements.
Table 6.1: Universal
Treatment Standards (UTS) for Reuse of Sediment Treated by Cement Mixing and
Stabilization
Parameters
|
TCLP Limit (mg/L)
|
Arsenic
|
5
|
Cadmium
|
0.11
|
Total Chromium
|
0.6
|
Lead
|
0.75
|
Mercury
|
0.025
|
Nickel
|
11
|
Zinc
|
4.3
|
Notes:
1) Universal Treatment Standard – US 40
CFR 268.48
2)
Antimony and Barium are
excluded from the above table as they are not considered as a contaminant of
concern for the sediment quality in the EIA study. For Copper, it must be
reduced by at least 90% in mobility for copper through cement stabilization/solidification
remedial treatment. The reduction of mobility of copper (leachable metals
contaminant) should be confirmed through TCLP tests (i.e.
to carry out TCLP test for the untreated sediment and for the sediment after
treatment and to compare the concentrations of copper in the leachates). By
taking account into the scenario where the Copper concentration of the sample
is below the limit of the reporting (LOR) of the laboratory analysis (Copper:
0.1 mg/L), the treatment target is considered to be
achieved in case the Copper concentration of the sample taken after treatment
is smaller than the LOR.
6.1.4 The testing frequency for TCLP is one sample per 50 m3
of the broken up solidified mixture of the treated marine sediment mix for the
first 1,000 m3 of the treated marine sediment. Provided that the
samples meet the UTS for the tested parameters shown in Table
6.1 and the UCS test, the subsequent testing frequency will be reduced
to be at least two samples per 10,000 m3. In the event that the
treated marine sediment mix does not meet the specified treatment target, the
concerned whole batch should be crushed and the
material would be further handled and treated as necessary. The testing
frequency should be revised to one sample per 50 m3 (with two
further samples kept for contingency) and treated samples should be taken for
laboratory testing. Once the UTS and UCS for the relevant tested parameters are
attained, the previous sampling frequency should be resumed
6.1.5 In the worst case scenario where
cement/solidification/stabilization techniques cannot achieve the specified
treatment target of the excavated marine sediment, the Contractor shall propose
alternative method(s) to treat the marine sediment. The Contractor shall seek
review without objection from the ET and IEC, and acceptance by EPD on the
proposed alternative method(s).
6.2
Mitigation
Measures
6.2.1 The proposed mitigation measures are summarised in the EMIS
in Appendix B.
7 Waste
Management
7.1
General
7.1.1 Measures including the opportunity for on-site sorting,
reusing excavated materials for reclamation etc, are devised in the
construction methodology to minimise the surplus materials to be disposed
off-site. Proper disposal of chemical waste should be via a licensed waste
collector.
7.1.2 EM&A requirements for waste management are only required
during the construction phase. Effective management of waste during the
construction phase shall be monitored through site audit programme. The aims of
the waste audit are:
·
to ensure the waste arising from the works are handled, stored,
collected, transferred and disposed of in an
environmentally acceptable manner; and
·
to encourage the reuse and recycling of material.
7.1.3 A trip-ticket system should be operated to monitor all
movements of chemical wastes which will be collected by a licensed collector to
a licensed facility for final treatment and disposal.
7.2
Waste EM&A
Requirements
7.2.1 The Contractor shall be required to pay attention to the
environmental standard and guidelines and carry out appropriate waste
management and obtain the relevant licence/permits for waste disposal.
The ET shall ensure that the Contractor has obtained from the appropriate
authorities the necessary waste disposal permits or licences including:
·
Billing account under the Waste Disposal (Charge for Disposal of
Construction Waste) Regulation (Cap 354N);
·
Chemical Waste Permits/licenses under the Waste Disposal Ordinance (Cap
354C);
·
Public Dumping License under the Land (Miscellaneous Provisions)
Ordinance (Cap 28); and
·
Effluent Discharge License under the Water Pollution Control Ordinance.
7.2.2 The Contractor shall refer to the relevant booklets issued
by the EPD when applying for the licence/permit and the ET shall refer to these
booklets for auditing purposes.
7.2.3 During the site inspections and the document review
procedures, the ET shall pay special attention to the issues relating to waste
management and check whether the Contractor has followed the relevant contract
specifications and the procedures specified under the laws of Hong Kong. In
addition to the site inspections, the ET shall review the documentation procedures
prepared by the Contractor once a week to ensure proper records are being
maintained and procedures undertaken in accordance with the Waste Management
Plan.
7.2.4 The Contractor’s waste management practices shall be audited
with reference to the checklist detailed in Table 7.1
below:
Table 7.1: Waste Management
Checklist
Activities
|
Timing
|
Monitoring Frequency
|
Action Required if non-compliance
|
All necessary waste disposal permits/ licences have been
obtained.
|
Before commencement of works
|
Once
|
Apply for the permits/ licences prior to disposal of waste. The ET
shall ensure that corrective actions are taken.
|
Only licensed waste hauliers are used for waste collection.
|
Throughout the works
|
Weekly
|
The ET shall inform PM and IEC of the non-compliance. The
PM shall instruct the Contractor to use a licensed waste haulier. The
Contractor shall temporarily suspend waste collection of that particular waste until a licensed waste haulier is
used. Corrective action shall be undertaken within 48 hours.
|
Records of quantities of waste generated, reused, recycled, and
disposed are properly kept. For construction and demolition material/ waste,
number of loads each day shall be recorded. *
|
Throughout the works
|
Weekly
|
The Contractor shall estimate the missing data based on previous
record and the activities carried out. The ET shall audit the results and
forward to PM and IEC for approval.
|
Waste are removed from site in a timely
manner.
|
Throughout the works
|
Weekly
|
The ET shall inform PM and IEC of the non-compliance. The PM
shall instruct the Contractor to remove waste accordingly.
|
Waste storage areas are properly cleaned and do not cause
windblown litter and dust nuisance.
|
Throughout the works
|
Weekly
|
The ET shall inform PM and IEC of the non-compliance. The PM
shall instruct the Contractor to clean the storage and/or properly cover the
waste storage areas.
|
Waste of different types is segregated in different containers
or skip to enhance recycling of material and proper disposal of waste.
|
Throughout the works
|
Weekly
|
The ET shall inform PM and IEC of the non-compliance. The PM
shall instruct the Contractor to provide separate containers/ skips for
different types of waste and ensure the workers place the waste in
appropriate containers.
|
Chemical waste is stored, handled, and disposed of in accordance
with the Code of Practice on the Packaging, Handling and Storage of Chemical
Wastes published by EPD.
|
Throughout the works
|
Weekly
|
The ET shall inform PM and IEC of the non-compliance. The PM
shall instruct the Contract to rectify the problems immediately. Warning
shall be given to the Contractor if corrective actions are not taken within
24 hours and the Waste Control Group of the EPD shall be notified.
|
Construction and demolition material/ waste in dump trucks are
properly covered before leaving the site.
|
Throughout the works
|
Weekly
|
The ET shall inform PM and IEC of the non-compliance. The PM
shall instruct the Contractor to comply. The Contractor shall prevent trucks
shall leaving the site until the waste are properly covered.
|
Waste is disposed of at licensed sites.
|
Throughout the works
|
Weekly
|
The ET shall inform PM and IEC of the non-compliance. The PM
shall warn the Contractor and instruct the Contractor to ensure the wastes
are disposed of at the licensed sites. Should it involve chemical waste, the
Waste Control Group of EPD shall be notified.
|
Note: * Quantity of waste can be estimated based on average
truck load and the details of the billing account of the Contractor under the
Waste Disposal (Charges for Disposal of Construction Waste) Regulation.
|
7.3
Mitigation
Measures
7.3.1 All the relevant mitigation measures for the Project
recommended in the EIA Report are summarised in the EMIS in Appendix B.
8 Water
Quality
8.1
General
8.1.1 As the construction works of the Project will be land-based,
the key water quality issues of the Project include water quality impacts from
construction site runoff, and wastewater and sewage generated from construction
activities. Mitigation measures are recommended in the EIA Report for
controlling potential water pollution from land works and are considered
relevant and adequate for the Project.
8.1.2 Prior to the commencement of the construction work, a
detailed site drainage management plan should be prepared by the
Contractor. The plan should cover measures to minimize all potential
water quality impact arising from the surface runoffs of the Project. The plan
shall be reviewed by ET and IEC before submission to EPD.
8.2
Mitigation
Measures
8.2.1 The construction water quality control measures recommended
in the EIA Report such as preventing direct discharge of wastewater from
temporary site facilities, providing storm drainage with silt removal
facilities, controlling site surface runoff, preventing oil and chemical
spillage, and other measures outlined in the Practice Note for Professional
Persons (ProPECC), Construction Site Drainage (PN
1/94) should be adopted to control any potential water quality impacts.
Mitigation measure to minimise water quality impacts from construction site
runoff and wastewater and sewage generated from construction activities
include:
(i) Provision
of site drainage systems over the entire construction site with sediment
control facilities. Regular inspection and maintenance of the site
drainage systems are required to ensure proper and efficient
operation at all times.
(ii) Sediment-laden
wastewater generated from foundation construction work, wheel washing, site
runoff and wastewater with high concentration of SS as generated from any
construction activities should be treated using sedimentation tanks or package
treatment systems. Treated wastewater can be reused for vehicle washing,
dust suppression and general cleaning. Bentonite slurry used in bore-pile
construction should be reconditioned and reused to minimise the disposal volume
of the used slurry.
(iii) The construction programme
should be properly planned to avoid soil excavation in rainy seasons. Exposed
stockpiles of excavated soils or construction materials should be covered with
tarpaulin or impervious sheets to avoid release of pollutants into the drainage
channels.
(iv) Licensed waste collector
should be employed for the collection and disposal of the sewage generated from
portable toilets.
(v) Wheel washing
facilities should be installed at all site entrances/exits.
(vi) An emergency plan should be developed
by the Contractor to deal with accidental spillage of chemicals.
8.2.2 A license under the Water Pollution Control Ordinance should
be obtained prior to any discharge of wastewater under the Project. All
discharge should be in compliance with the conditions
as stipulated in the license.
8.2.3 All the relevant mitigation measures recommended in the EIA
Report are summarised in the EMIS in Appendix B.
9 Ecology
9.1
General
9.1.1 The construction works of the Project will be undertaken on
reclaimed land with no existing terrestrial ecological habitat. No
potential ecological impact associated with the Project works is identified and
therefore no mitigation measures are required.
10 Fisheries
10.1 General
10.1.1 As the construction works of the Project will be undertaken
on reclaimed land, no potential impacts related to fisheries and marine culture
were identified and therefore no mitigation measures are required.
11 Cultural Heritage
11.1 General
11.1.1 The Project works locate on reclaimed land with no existing
cultural heritage resources. No adverse impact on built heritage, marine
archaeology, and terrestrial archaeology is anticipated. Hence, further investigation
or mitigation measure is not required.
12 Hazard To
Life
12.1 General
12.1.1 No blasting work will be involved for the construction of
the Project. Therefore, no explosives Quantitative Risk Assessment (QRA) was undertaken and no mitigation measures is required.
13 Landscape & Visual
13.1 General
13.1.1 A number of design measures, such as
aesthetic architectural on related infrastructure, streetscape elements,
landscape planting and other measures including night-time lighting control
were recommended in the EIA Report for minimizing landscape and visual impacts
from the HKBCF project. This section outlines the relevant monitoring and audit
of these measures applicable to this Project.
13.2 Monitoring Details
13.2.1 The design, implementation and maintenance of landscape
mitigation measures should be checked by ET to ensure that any potential
non-conformity between the proposed landscape measures and any other works of
the project shall be resolved as early as practical without affecting the
implementation of the mitigation measures.
Table 13.1: Monitoring Programme
Stage
|
Monitoring
Task
|
Monitoring
Report
|
Form
of Approval
|
Frequency
|
Detailed Design**
|
Checking of design works against the recommendations of the landscape
and visual impact assessments within the EIA should be undertaken during
detailed design phase, to ensure that they fulfil the intention of the mitigation
measures. Any changes to the design,
including design changes on site should also be checked.
|
Not Required
|
Not Required
|
At the end of Detailed Design Phase
|
Construction *
|
Checking of the contractor’s protection and mitigation measures during
the construction period.
|
Report on Contractor’s compliance, by ET
|
Counter-signature of report by IEC
|
Bi-weekly
|
Establishment Works *
|
Checking of the maintenance of existing trees and landscape planting
works during the 12-month Establishment Period after completion of the
construction works.
|
Report on Contractor’s compliance by Maintenance Agency as appropriate
|
Counter-signature of report by Management
Agency
|
Every two months
|
Long Term Management (10 year) *
|
Monitoring of the long-term management of the landscape planting works
in the period up to 10 years after completion of the construction works
|
Report on Contractor’s compliance by Maintenance Agency as appropriate
|
Counter-signature of report by Management
Agency
|
Annually
|
Notes:
* During the construction, establishment and long-term
management phases, the management and maintenance of existing trees are
provided by the Management, Operation and Maintenance (MOM) Contractor and HyD Contract No. HY/2019/01.
** The detailed design of HKIA-HKBCF Road Connection was
completed.
|
Detailed
Design Phase
13.2.2 The relevant mitigation measures, which were proposed in the
EIA Report to mitigate the landscape and visual impacts, were embodied into the
detailed engineering design, landscape design drawings and contract
documents. The Detailed Design were checked to ensure that the measures
are fully incorporated. The agent for implementation and checking of the
measures are summarized in EMIS in Appendix B.
13.2.3 The following mitigation measures were proposed to avoid and
reduce the identified impacts:
·
Minimize the footprint of project and that the quantity of landscape
character units and landscape resources affected;
·
Minimize temporary works areas for construction works;
·
Undertaking good site practices by applying hydroseeding on temporary
stockpiles and reclamation areas;
·
Conservation of topsoil for reuse; and
·
Waste limitation by recycling of felled trees into woodchip mulch for
use in landscaped areas.
13.2.4 The following design measures were developed during detailed
design stage to remedy and compensate unavoidable impacts:
·
Protection measures for the trees to be retained during construction activities;
·
Optimizing the sizes and spacing of the bridge columns;
·
Fine-tuning the location of the bridge columns to avoid visually-sensitive locations; and
·
Maximizing new tree, shrub and other vegetation
planting to compensate tree felled and vegetation removed.
Construction
Phase and Establishment Period
13.2.5 The following mitigation measures should be monitored during
construction and operation phases:
Table
13.2: Mitigation Measures during Construction and Operation Phases
Stage
|
Description
of Mitigation Measures
|
Construction Phase
|
Mitigate both
Landscape and Visual Impacts
G1.
Grass-hydroseed bare soil surface and stock pile
areas.
G2. Add planting
strip and automatic irrigation system if appropriate at some portions of
bridge or footbridge to screen bridge and traffic.
G11. All existing
trees shall be carefully protected during construction.
|
Mitigate Visual
Impacts
V1. Minimize time
for construction activities during construction period.
V2. Provide screen
hoarding at the portion of the project site / works areas / storage areas
near Visual Sensitive Receivers (VSRs) who have close low-level views to the
Project during construction.
|
Operation Phase
|
Mitigate both
Landscape and Visual Impacts
G10. Provide proper
planting maintenance on the new planting areas to enhance the aesthetic
degree.
|
Mitigate Visual
Impacts
V3. Lighting
design to minimize glare at night.
Decorative road lighting to be considered during detailed design
stage.
|
13.2.6 During the construction, establishment and long-term
management phases, the management and maintenance of existing trees are
provided by the MOM Contractor and HyD Contract No.
HY/2019/01. The remaining landscape and visual mitigation measures are provided
by the Contractor of AAHK as stated in Table 13.2.
13.2.7 Measures to mitigate landscape and visual impacts during
construction should be checked to ensure compliance with the intended aims of
the measures.
13.2.8 The progress of the engineering works shall be regularly
reviewed on site to identify the earliest practical opportunities for the
landscape works to be undertaken.
Long
Term Management (10 Years)
13.2.9 The management and maintenance of existing trees will be
provided by the MOM Contractor and HyD Contract No.
HY/2019/01 during the first 10 years of the operation phase of the Project. Any
areas of vegetation which is failed to establish, should be corrected by the
relevant maintenance parties at the earliest opportunity. The maintenance requirement of the planting
works stated in the Long Term Management stage is
included in the monitoring requirement.
13.3 Baseline Monitoring
13.3.1 A photographic record of the site at the time of the
Contractor’s possession of the site shall be prepared by the Contractor and
approved by the PM. The approved photographic record shall be submitted to the
PM, ET and IEC for record.
13.4 Event and Action Plan for
Landscape and Visual Works
Table 13.3: Event and Action Plan
Event
|
Action
|
|
ET
|
IEC
|
PM
|
Contractor
|
Non-conformity occur
|
· Check Contractor’s proposed remedial design conforms to the requirements
of EP and prepare checking report(s)
|
· Check and endorse ET’s report(s)
· Check and certify Contractor’s proposed
remedial design
|
· Supervise the Contractor to carry out the proposed
remediation work
|
· Propose remedial design and carry out the
proposed remediation work
|
13.5 Mitigation Measures
13.5.1 The mitigation measures as recommended in the EIA Report are
summarised in the EMIS in Appendix B.
14 Site Environmental Audit
14.1 General
14.1.1 Site inspection provides a direct means to initiate and
enforce specified environmental protection and pollution control
measures. These shall be undertaken routinely to inspect construction
activities in order to ensure that appropriate
environmental protection and pollution control mitigation measures are properly
implemented. Site inspection is one of the most effective tools to
enforce the environmental protection requirements at the works area.
14.1.2 The ET Leader shall be responsible for formulating the
environmental site inspection, the deficiency and action reporting system, and
for carrying out the site inspection works. Within 21 days of the
construction contract commencement, he shall submit a proposal for site
inspection and deficiency and action reporting procedures to the IEC for
agreement, and to PM for approval. The Contractor’s proposal for
rectification shall be made known to ET, IEC and PM.
14.1.3 Regular site inspections shall be carried out at least once
per week. The areas of inspection shall not be limited to the
environmental situation, pollution control and mitigation measures within the
site. It should also review the environmental situations outside the
works area which is likely to be affected, directly or
indirectly, by the site activities. The ET Leader shall make reference to the following information in conducting
the inspection:
(i) EIA recommendations on
environmental protection and pollution control mitigation measures;
(ii)
Works progress
and programme;
(iii)
Individual works
methodology proposals (which shall include proposal on associated pollution
control measures);
(iv)
Contract
specifications on environmental protection;
(v)
Relevant environmental
protection and pollution control laws; and
(vi)
Previous site
inspection results.
14.1.4 The Contractor shall keep the ET Leader updated with all
relevant information on the construction contract necessary for him to carry
out the site inspections. Inspection results and associated
recommendations for improvements to the environmental protection and pollution
control works shall be submitted to the IEC and the Contractor within 1 working
day. The Contractor shall follow the procedures and time-frame
as stipulated in the environmental site inspection, and the deficiency and
action reporting system formulated by the ET Leader, to report on any remedial
measures subsequent to the site inspections.
14.1.5 Ad-hoc site inspections shall also be carried out if
significant environmental problems are identified. Inspections may also
be required subsequent to receipt of an environmental
complaint, or as part of the investigation work, as specified in this Manual.
14.2 Compliance with Legal and
Contractual Requirements
14.2.1 There are contractual environmental protection and pollution
control requirements as well as environmental protection and pollution control
laws in Hong Kong with which construction activities must comply.
14.2.2 In order that the works comply with the contractual
requirements, all works method statements submitted by the Contractor to PM for
approval shall be sent to the ET Leader for vetting to ensure sufficient
environmental protection and pollution control measures have been
included. The implementation schedule of mitigation measures is
summarised in Appendix B.
14.2.3 The ET Leader shall also review the progress and programme
of the works to check that relevant environmental laws have not been violated,
and that any foreseeable potential for violating laws can be prevented.
14.2.4 The Contractor shall regularly copy relevant documents to
the ET Leader so that checking can be carried out. The document shall at
least include the updated Works Progress Reports, updated Works Programme, any
application letters for different licence / permits under the environmental
protection laws, and copies of all valid licences / permits. The site
diary shall also be available for the ET Leader's inspection upon his
request.
14.2.5 After reviewing the document, the ET Leader shall advise the
IEC and Contractor of any non-compliance with contractual and legislative
requirements on environmental protection and pollution control for them to take
follow-up actions. If the ET Leader's review concludes that the current status on licence / permit application and any
environmental protection and pollution control preparation works may result in
potential violation of environmental protection and pollution
control requirements, he shall also advise the Contractor and PM
accordingly.
14.2.6 Upon receipt of the advice, the Contractor shall undertake
immediate actions to correct the situation. The PM shall follow up to
ensure that appropriate action has been taken in order to
satisfy contractual and legal requirements.
14.3 Environmental Complaints
14.3.1 Complaints shall be referred to the ET Leader for
action. The ET Leader shall undertake the following procedures upon
receipt of any complaint:
(i) log complaint and date of
receipt onto the complaint database and inform the IEC immediately;
(ii) investigate the complaint to determine
its validity, and assess whether the source of the problem is due to works activities;
(iii) identify mitigation measures
in consultation with the IEC if a complaint is valid and due to works;
(iv) advise the Contractor if
mitigation measures are required;
(v) review the Contractor's
response to identified mitigation measures, and the updated situation;
(vi) if the complaint is
transferred from the EPD, submit interim report to the EPD on status of the
complaint investigation and follow-up action within the time frame assigned by
the EPD;
(vii) undertake additional
monitoring and audit to verify the situation if necessary, and review that circumstances leading to the complaint do not recur;
(viii) report investigation results and
subsequent actions to complainant (if the source of complaint is EPD, the
results should be reported within the timeframe assigned by the EPD); and
(ix)
record the
complaint, investigation, the subsequent actions and
the results in the monthly EM&A reports.
15 Reporting
15.1 General
15.1.1 Reports can be provided in an electronic medium upon
agreeing the format with PM and EPD. This would enable a transition from
a paper / historic and reactive approach to an electronic / real time proactive
approach.
15.1.2 The ET is responsible for establishing and maintaining a
dedicated website throughout the entire construction period for publishing all
the relevant finalized submissions and plans as required under the FEP.
The ET shall propose the format and functionality of the website for agreement
with PM and IEC prior to publishing of the submissions and plans. Once the
environmental submissions and plans are available and vetted by the IEC, the ET
is responsible to upload the relevant documents to the dedicated
website.
15.1.3 Types of reports that the ET shall prepare and submit
include monthly EM&A report, quarterly EM&A report
and final EM&A review report. A copy of the monthly, quarterly and final EM&A review reports shall be made
available to the Director of Environmental Protection.
15.2 Monthly EM&A Reports
15.2.1 The results and findings of all EM&A work required in
the Manual shall be recorded in the monthly EM&A reports prepared by the ET
Leader. The EM&A report shall be prepared and submitted within 10
working days of the end of each reporting month, with the first report due the
month after construction commences. Each monthly EM&A report shall be
submitted to the following parties: the IEC, PM and EPD. Before the
submission of the first EM&A report, the ET Leader shall liaise with the
parties on the required number of copies and format of the monthly reports in
both hard copy and electronic medium.
First
Monthly EM&A Report
15.2.2 The first monthly EM&A report shall include at least the
following:
(i) Executive summary (1-2
pages):
·
complaint log;
·
notifications of any summons and successful prosecutions;
·
reporting changes; and
·
future key issues.
(ii)
Basic project
information:
·
project organisation including key personnel contact names and telephone
numbers;
·
programme;
·
management structure, and
·
works undertaken during the month.
(iii)
Environmental
status:
·
works undertaken during the month with illustrations (such as location
of works, major site works, etc); and
·
drawings showing the project area.
(iv)
A
brief summary
of EM&A requirements including:
·
environmental mitigation measures relevant to the Project, as
recommended in the EIA Report; and
·
environmental requirements in contract documents.
(v)
Implementation
status:
·
advice on the implementation status of environmental protection and
pollution control / mitigation measures relevant to the Project, as recommended
in the EIA Report.
(vi)
Report on
non-compliance, complaints, and notifications of summons and successful
prosecutions:
·
record of all complaints received (written or verbal) for each media,
including locations and nature of complaints investigation, liaison and
consultation undertaken, actions and follow-up procedures taken, results and summary;
·
record of all notification of summons and successful prosecutions for
breaches of current environmental protection / pollution control legislation,
including locations and nature of the breaches, investigation, follow-up
actions taken, results and summary;
·
review of the reasons for and the implications of non-compliance,
complaints, summons and prosecutions including review
of pollution sources and working procedures; and
·
description of the actions taken in the event of non-compliance and
deficiency reporting and any follow-up procedures related to earlier
noncompliance.
(vii)
Others
·
an account of the future key issues as reviewed from the works programme
and work method statements;
·
advice on the solid and liquid waste management status; and
·
comments (for examples, effectiveness and efficiency of the mitigation
measures), recommendations (for example, any improvement in the EM&A
programme) and conclusions.
Subsequent
EM&A Reports
15.2.3 Subsequent monthly EM&A reports shall include the
following:
(i) Executive summary (1 - 2
pages):
·
complaints log;
·
notifications of any summons and successful prosecutions;
·
reporting changes; and
·
future key issues.
(ii)
Basic project
information:
·
project organisation including key personnel contact names and telephone
numbers;
·
programme;
·
management structure; and
·
work undertaken during the month.
(iii)
Environmental
status:
·
works undertaken during the month with illustrations (such as location
of works, major site works, etc.); and
·
drawing showing the project area.
(iv)
Implementation status:
·
advice on the implementation status of environmental protection and
pollution control / mitigation measures relevant to the Project, as recommended
in the EIA Report.
(v)
Report on
non-compliance, complaints, and notifications of summons and successful
prosecutions:
·
record of all complaints received (written or verbal) for each media,
including locations and nature of complaints investigation, liaison and
consultation undertaken, actions and follow-up procedures taken, results and summary;
·
record of all notification of summons and successful prosecutions for
breaches of current environmental protection / pollution control legislation,
including locations and nature of the breaches, investigation, follow-up
actions taken, results and summary;
·
review of the reasons for and the implications of non-compliance,
complaints, summons and prosecutions including review
of pollution sources and working procedures; and
·
description of the actions taken in the event of non-compliance and
deficiency reporting and any follow-up procedures related to earlier
noncompliance.
(vi)
Others
·
an account of the future key issues as reviewed from the works programme
and work method statements;
·
advice on the solid and liquid waste management status; and
·
comments (for examples, effectiveness and efficiency of the mitigation
measures), recommendations (for example, any improvement in the EM&A
programme) and conclusions.
(vii)
Appendices
·
cumulative statistics on complaints, notifications of summons and
successful prosecutions; and
·
outstanding issues and deficiencies.
15.3 Quarterly EM&A Reports
15.3.1 Quarterly EM&A reports shall include the
following:
(i) Executive summary (1 - 2
pages):
(ii) Basic project information:
·
project organization;
·
programme;
·
contacts of key management structure; and
·
work undertaken during the quarter.
(iii) Brief summary of EM&A
requirements:
·
environmental mitigation measures relevant to the Project, as
recommended in the EIA Report;
(iv) Advice on the implementation
status of environmental protection and pollution control / mitigation measures
relevant to the Project, as recommended in the EIA Report, summarised in the
updated implementation schedule;
(v) Drawings showing the project area;
(vi) Advice on the solid and
liquid waste management status;
(vii) A brief review of the reasons
for and the implications of any non-compliance, including a review of pollution
sources and working procedures;
(viii) A summary description of
actions taken in the event of non-compliance and any follow-up procedures
related to any earlier non-compliance;
(ix) A summarised record of all
complaints received (written or verbal) for each media, liaison and
consultation undertaken, actions and follow-up procedures taken;
(x) Comments (for examples, a
review of the effectiveness and efficiency of the mitigation measures and the
performance of the environmental management system, that is, of the overall
EM&A programme); recommendations (for example, any improvement in the
EM&A programme) and conclusions for the quarter; and
Project Proponent’s contacts and any hotline telephone number for the public to
make enquiries.
15.4 Final EM&A Review Reports
15.4.1 The final EM&A report should contain at least the
following information:
(i) Executive summary (1 - 2
pages);
(ii) Drawings showing the project area;
(iii) Basic project information
including a synopsis of the project organisation, contacts of key management,
and a synopsis of work undertaken during the course of the project or past
twelve months;
(iv) A brief
summary
of EM&A requirements including:
·
environmental mitigation measures relevant to the Project, as
recommended in the EIA Report; and
·
environmental impact hypotheses tested;
(v) A summary of the implementation
status of environmental protection and pollution control / mitigation measures
relevant to the Project, as recommended in the EIA Report, summarised in the
updated implementation schedule;
(vi) A review of the reasons for
and the implications of non-compliance including review of pollution sources
and working procedures as appropriate;
(vii) A description of the actions
taken in the event of non-compliance;
(viii) A summary record of all
complaints received (written or verbal) for each media, liaison and
consultation undertaken, actions and follow-up procedures taken;
(ix) A summary record of
notifications of summons and successful prosecutions for breaches of the
current environmental protection / pollution control legislation, locations and
nature of the breaches, investigation follow-up actions taken and results;
(x) Review of the validity of EIA
predictions and identification of shortcomings in EIA recommendations;
(xi) Comments (for examples, a
review of the effectiveness and efficiency of the mitigation measures and of
the performance of the environmental management system, that is, of the overall
EM&A programme); and
(xii) Recommendations and
conclusions (for example, a review of success of the overall EM&A programme
to cost-effectively identify deterioration and to initiate prompt effective
mitigation measures when necessary).
15.5 Document Keeping
15.5.1 No site-based documents are required to be included in the
monthly EM&A reports. However, any such document shall be well kept
by the ET Leader and be ready for inspection upon request. All relevant
information shall be clearly and systematically recorded in the document.
All documents shall be kept for at least one year following completion of the
construction contract.